Más de 2000 instalaciones en los 5 continentes avalan nuestra marca.
Ultrafiltración tangencial cerámica
En la ultra filtración tangencial cerámica (UFTC) se utiliza una barrera física y una bomba de presión que obliga a los sólidos en suspensión, bacterias, virus y otras sustancias contenidas en el agua, a circular tangencialmente por una superficie porosa encargada de llevar a cabo la separación física para producir una agua de alta pureza.
Esta tecnología se aplica para la separación de materias primas y sub-productos reutilizables, recuperación de agentes químicos utilizados durante el proceso industrial y depuración para el cumplimiento de los estándares de vertido. Actualmente, se utiliza con éxito en la industria cosmética, en la potabilización de aguas y la recuperación de fármacos, además de tener una gran proyección en la depuración de aguas de otros tipos de industrias como la alimentaria y la de los colorantes.
C&G IBERICA también ha desarrollado proyectos muy específicos en la industria galvánica, para el mantenimiento de laca cataforética.
DESCRIPCIÓN TÉCNICA
El proceso de ultrafiltración tangencial cerámica (UFTC) se aplica en procesos donde encontramos un influente industrial con un alto nivel de carga. En estos casos donde los reactores biológicos tradicionles necesitan un tiempo considerable para degradar la materia, es preferible realizar una separación previa de los residuos, para facilitar posteriormente una degradación biológica rápida y de calidad.
El equipo de UFTC se compone principalmente de dos depósitos de acumulación, un sistema de bombeo de presión y los filtros cerámicos. Existe un sistema hidráulico secundario que se encarga de limpiar las membranas a contracorriente para mantener el rendimiento del sistema.
RETENIDO: es donde se realiza la entrada de aguas mediante una sonda de nivel y se van aportando a medida que el circuito cerrado se va vaciando debido a la salida de aguas filtradas.
BOMBA: realiza la recirculación de aguas a la velocidad tangencial requerida por el fabricante de las membranas
FILTRO UFTC: se realizan los dos flujos separativos, por un lado el filtrado y por otro el retenido.
FILTRADO: depósito de agua filtrada donde realizamos el almacenamiento de las mismas para lavado a contra corriente, o bien para limpiezas químicas cuando se requieran.
Como podemos apreciar en la ilustración lateral, que representa un filtro de membranas cerámicas, el flujo de entrada lo hace de forma axial, con lo cual las partículas inciden de forma tangencial a la membrana. Este hecho provoca una separación de las partículas de agua (azules) de las demás (rojas). Así pues, separamos el caudal de entrada en una salida de concentrado/retenido y el agua filtrada.
Las principales ventajas del sistema de UFTC es que permite una separación de contaminantes para aguas de origen industrial altamente cargadas, reteniendo subfracciones importantes, pero pudiendo mantener la actividad biológica posterior mediante sistema tradicional de depuración por lodos activos, biológico o bien por un bioreactor con membranas (MBR).
Las membranas cerámicas tienen una alta resistencia química, mecánica y estabilidad térmica, una alta duración y pueden efectuar retrolavados con aire o productos químicos altamente corrosivos, con lo cual siempre disponemos de una óptima capacidad de filtración, lo cual se traduce en un efluente resultante de alta calidad.
ULTRAFILTRACIÓN TUBULAR
El proceso de Ultrafiltración tubular se utiliza principalmente para dos actividades. En primer lugar podemos encontrarnos con depuradoras en donde no existe un reactor biológico, pero si un sistema secundario de tratamiento, por otro lado también se puede aplicar en aguas superficiales, como lagos, ríos o pozos.
Para las aguas de origen urbano o industrial, la aplicación de la ultrafiltración tubular nos permite disponer de un efluente con una calidad apta para la reutilización. Mientras que para las aguas superficiales, el tratamiento con ultrafiltración posibilita el uso potable del agua tratada.
Como podemos ver en el esquema inferior, el equipo de ultrafiltración tubular se dispone en serie con los demás elementos de la instalación, de tal manera, que por un lado se consigue agua clarificada y por el otro residuo sólido de desecho.
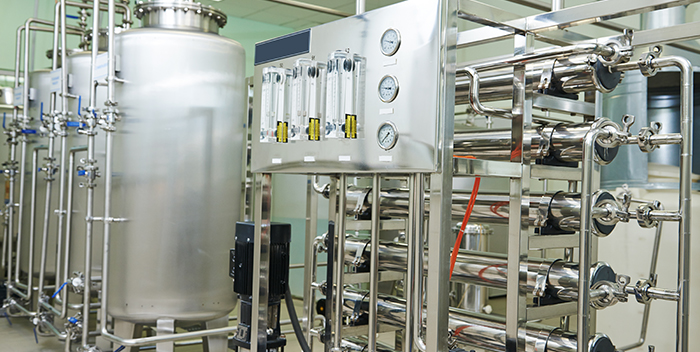
OSMOSIS INVERSA
Introducción
El proceso de Osmosis Inversa utiliza membranas semipermeables para separar el agua de los contaminantes: sólidos disueltos, productos orgánicos e inorgánicos, virus, bacterias, etc.
El proceso se conoce como osmosis" inversa", ya que es necesaria una presión externa para obligar al agua pura a atravesar una membrana, dejando atrás las impurezas. La osmosis inversa es capaz de separar entre el 95%-99% de los sólidos disueltos totales (TDS) y el 99% de todas las bacterias, produciendo así agua pura y de muy baja mineralización.
En principio, cualquier tipo de agua puede ser tratada con la osmosis inversa. Para sacarle el mayor rendimiento a esta tecnología, a menudo hace falta tratar el agua, antes de pasarla por las membranas de osmosis inversa. En muchos casos, esto es necesario porque las membranas con las que trabaja la osmosis inversa son muy sensibles y tienden a obstruirse.
Para evitar frecuentes lavados o sustituciones de las membranas, generalmente son efectuados pre-tratamientos del tipo: Descalcificadores (eliminación de dureza), filtración a carbón activo(eliminación sustancias orgánicas), Ultra-filtración(eliminación aceite y grasa), Evaporación (eliminación sal), etc.
Descripción general de funcionamiento
La bomba de osmosis (P1) aspira la solución que debe ser impulsada a 18¸20 bar, y la hace pasar a través de las membranas de osmosis inversa (M1, M2).
A través de estas membranas se produce una filtración de los iones presentes en el agua, el permeado que sale de las membranas, es agua de buena calidad, que puede ser re-utilizada.
El permeado, agua osmotizada, se almacena en un tanque de acumulación (T2), situado en la misma estructura del equipo, y desde aquí, es enviado hasta su lugar de aplicación a través de una bomba centrifuga (P2).
En el sistema vienen instalados:
- dos manómetros, para poder visualizar el grado de obstrucción de las membranas
- un presostato de alta presión, que pararía el equipo por alarma
- dos caudalimetros que permiten ver el flujo en l/h de concentrado (rechazo) y del permeado (agua osmotizada) producidos en el proceso.
FUNCIÓN DE LOS COMPONENTES PRINCIPALES
Bomba de Osmosis “P1” Aspira el agua del tanque de recoleccion “T1” y la envía a las membranas osmóticas. Con esta bomba de alta presión, se pueden alcanzar los flujos (caudal) y la presión necesaria, para obtener la cantidad de permeado que se necesita. Esta bomba está dotada de un control de nivel “LC1” que evita su funcionamiento en seco.
Bomba de lavado y re-envío del permeado “P2” Aspira el agua osmotizada acumulada en el tanque “T2” y la envía a un tanque de reserva para su re-utilización.. El control de nivel “LC2” evita su funcionamiento en seco.
Esta bomba es también utilizada para todas las operaciones de mantenimiento y lavado de las membranas.
Pre-Filtro “F1” Se instala antes de la bomba de osmosis para evitar que algunas partículas nocivas dañen la bomba.
Membranas Osmóticas “M1” e “M2” Efectúan la de-ionizacion del agua aprovechando el principio de la osmosis inversa. Para el control del estado de obstrucción vienen instalados dos manómetros “PI1” e “PI2”; mientras que para su seguridad, se instala un presostato “PC” tarado a 20 bar.
Aplicaciones
A día de hoy, la tecnología de osmosis inversa tiene un sinfín de aplicaciones, entre las cuales cabe destacar: potabilización del agua, racionalización de los ciclos productivos, ahorro energético, descontaminación, recuperación de las aguas y sustancias de interés para el ciclo productivo.
Sectores industriales donde se aplica esta tecnología:
- Producción de agua potable.
- Producción de agua para generadores de vapor.
- Producción de agua ultra-pura para la industria Electrónica y de semiconductores.
- Industria Cosmética y farmacéutica (antibióticos, insulina, amino ácido, etc.),
- Alimentaria (zumos de frutas, sangre de animales, etc.).
- Tratamiento de residuos de la industria galvánica con recuperación de sales metálicas.
- Hospitales y laboratorios.
Biorreactor de membrana (MBR)
La tecnología de biorreactor de membrana (MBR) se basa en la combinación de un reactor biológico de biomasa suspendida, responsable de la degradación de los compuestos orgánicos, y una separación por filtración de membrana porosa, encargada de llevar a cabo la separación física mediante diferencia de presión entre los dos lados de la membrana.
Esta tecnología presenta una serie de ventajas en términos de protección de los recursos hídricos gracias a la gran calidad del agua tratada. La calidad del agua, en particular la ausencia de sólidos en suspensión y turbidez, permite considerar el MBR como una herramienta perfecta para el tratamiento previo antes de la desalinización o la preparación de agua de muy alta calidad. Por otra parte, debido a su propiedad modular, el MBR puede también ser favorable para el desarrollo de una nueva configuración de la red de aguas residuales en una zona urbana.
Las principales utilizaciones de la tecnología MBR son aumentar la capacidad y mejorar la calidad del agua en plantas convencionales ya existentes, y la posible reutilización de parte o de la totalidad del agua depurada. Es ideal para plantas con poca superficie disponible.
Esta tecnología es aplicable a varios sectores, y se han obtenido resultados excelentes en industrias tan dispares como la industria alimentaria y la industria cosmética.
DESCRIPCIÓN TÉCNICA
La depuración mediante MBR (Biorreactor de membrana) es un proceso de fangos activados en el cual el agua depurada no se extrae por sedimentación en un decantador secundario, sino por filtración a través de membranas. Así pues, se trata de un conjunto de reactor biológico juntamente con una ultrafiltración posterior.
Existen principalmente dos tipologías de membranas para MBR según su situación.
MEMBRANAS EXTERNAS O CON RECIRCULACIÓN AL BIOREACTOR
Esta configuración de MBR implica que el agua es recirculada, mediante una bomba eléctrica, desde el bioreactor hasta la unidad de membrana que se dispone externamente a la unidad biológica. Una parte del agua se filtra mientras que la otra se reenvía al reactor para que siga degradando las partículas orgánicas. Este tipo de membranas son tubulares y necesitan ser limpiadas a contracorriente con un sistema automatizado.
MEMBRANA SUMERGIDA
La unidad de membrana que realiza la separación física está inmersa en el tanque biológico. La fuerza impulsora a través de la membrana es alcanzada presurizando el bioreactor o creando presión negativa en el lado permeado. La limpieza de la membrana se realiza a través de frecuentes retrolavados con agua permeada y aire y ocasionalmente mediante retrolavados con soluciones químicas.
El balance económico es favorable a los MBRs si se tienen en cuenta una serie de ventajas importantes, al margen de la excelente calidad de agua tratada que se consigue.
De este modo, la tecnología MBR es especialmente competitiva cuando aparece alguno de los siguientes condicionantes:
- Necesidad de disminuir la producción de fangos biológicos (hasta un 80%)
- Necesidad de un grado de depuración elevado: vertido a cauce público, zonas sensibles o pago de un canon de vertido elevado.
- Reutilización: la reutilización puede venir impuesta por la escasez de agua de la zona o puede suponer un valor añadido importante a considerar. Las variables aquí van a ser el precio del metro cúbico de agua o las subvenciones por reutilización.
- Poco espacio disponible
- Ampliación de la capacidad de tratamiento de plantas convencionales ya existentes.
- Efluentes industriales con componentes de difícil o lenta biodegradabilidad. La tecnología MBR permite llegar a depurar materia orgánica considerada poco biodegradable para otro tipo de tecnologías más convencionales.